Note to our email subscribers: To view this post on our website (recommended), click here.
Things were moving fast inside the house last week. First up, the tape and mud crew came back to sand and smooth the walls and in some cases mud over areas. The gentleman above made walking on stilts look easy, he even climbed stairs. And then he was reaching above his head sanding, marking areas that needed attention and mudding. I have trouble walking in my Keens.
We met with Brian and Ron Moore, the trim guy who is also the window and door guy, Tuesday morning and walked through the house. On Wednesday we had a two hour meeting with Joe Sopko, the steel guy, for final measurements on the fireplace cladding, bracket templates for the deck stanchions (because of the cantilevered steel beams it's more complex than you might think), and the steel shelf in the primary bath.
 |
Living room, facing east |
 |
Kitchen, facing south |
 |
Butler's pantry and refrigerator/pantry cabinet area, facing west |
Mid-week the "finish guys" came in and did the final sanding and touch up. There is one stubborn area in the kitchen ceiling that they had to take back to sheetrock, carve out and redo. They promised they would make sure it was perfect before the job was done. They covered the remaining windows and doors and started priming. In the photos above you can see the area on the ceiling where they cut out the seam and mended it. So far, no cracks.
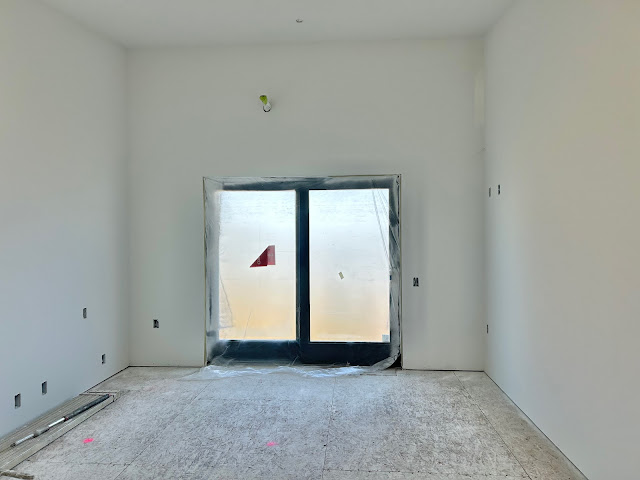 |
Primary bedroom, facing north |
 |
Primary bedroom, facing west |
I thought priming was the job of the painters, but apparently the sheet rock guys aren't finished until they have a smooth primed surface. Seriously, everyone had their undies in a bundle over the Level 4 smooth finish. It's the standard in the midwest where we're from, so we didn't understand that it's a big deal in the PNW. They have to finish the second floor, stairwell and then tackle the first floor and garage. Hopefully they'll be done by the end of next week.
We had some unseasonably nice weather this week so the solar guys showed up on Thursday, Friday and Saturday to get the solar panels installed, 30 total, and the wiring run from the roof into the garage.
And here we are with all the panels installed! I failed to take a photo of the wires in the garage today, so I'll update with those photos next week. They won't move the truck until the wiring is complete because there are some final steps they need to do on the roof right before they finish. Honestly, as excited as we were that the truck arrived, we can't wait for the truck to be gone.
You may notice in the photo above the small blob above the wire. After I took the photo with my iPhone I looked up and saw the bald eagle and hoped I had captured it in the picture.
Yes! Not that it's a grand photo by any means but we have seen this eagle before. We think there's a nest in the trees to the northwest of the house. I was able to photograph it a couple of weeks ago. It was a foggy day and we were meeting with the painter and Scott noticed it perched on the evergreen to the northwest of the house. Hopefully we can watch a lot more eagle activity this spring!